Unforeseen equipment failure in factories results in substantial losses from downtime, scrap, and overtime pay. But what if failures could be prevented before they happen? The way that manufacturers can achieve this is through predictive maintenance. Using predictive maintenance techniques means companies can drastically cut their costs.
What is Predictive Maintenance?
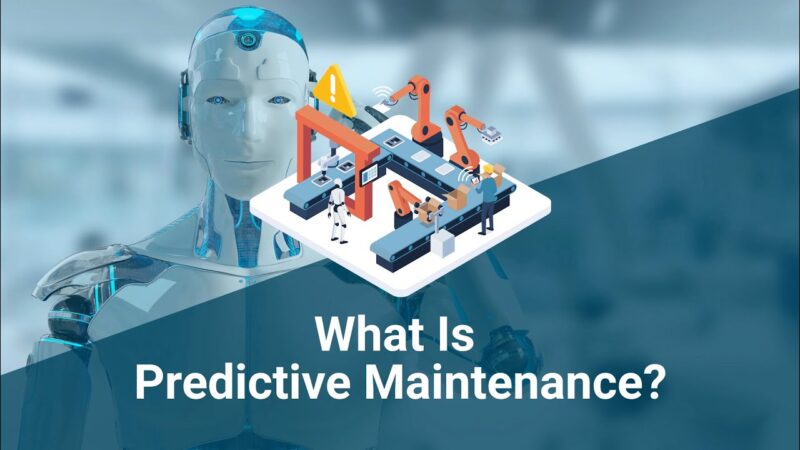
Predictive maintenance is about monitoring equipment for signs of trouble to prevent future problems. Sensors in the equipment can pick up warning signs that something is going off track before it fully breaks down. The system can alert staff to an issue with enough time to proactively address it. This prevents the problem from escalating into a more serious failure.
Predictive maintenance allows issues to be fixed when it’s convenient instead of unexpectedly in the middle of the night or a big job. It means more uptime in production and less money wasted dealing with breakdowns or replacing ruined materials.
Monitoring Health Remotely with IoT
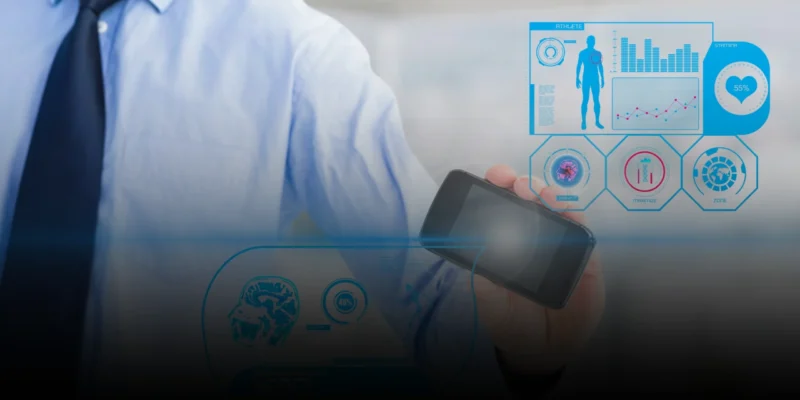
New remote monitoring IoT (internet of things) technologies make predictive maintenance more powerful than ever before. According to the good folk at Blues.com, IoT sensors can be installed directly inside of assets, where they continually check stats like vibration, temperature, and pressure. The sensors automatically transmit this data to the cloud through wireless connectivity.
Dashboard software then analyzes the massive data in real-time using machine learning algorithms to detect anomalies. Teams can access the dashboard from anywhere via computer or smartphone to see visual updates on the health status of all their connected assets. They get immediate notifications if the algorithms spot indicators an issue may arise, even before it’s perceptible to humans. This allows failures to be averted before downtime results.
Integrating advanced analytics and artificial intelligence further enhances the capability of these systems. Machine learning models can identify complex patterns and correlations that might escape traditional analysis methods. This deeper insight enables more accurate predictions and fewer false alarms.
Benefits of a Predictive Maintenance Program
Facilities that implement predictive maintenance see a multitude of cost savings in various areas. Here are some of the biggest benefits.
Less Downtime
Because warning signals are caught early on, teams can schedule repairs at opportune moments instead of forcing abrupt work stoppages that halt critical production. This allows for more operational uptime and reliable output levels.
Higher Product Quality
Worn-down equipment more frequently produces subpar products that end up getting scrapped. Restoring machinery to optimal condition before tolerance limits are breached means manufacturers avoid churning out rejects.
Fewer Emergency Fixes
Diagnosing and fixing surprise breakdowns during off-hours requires calling in workers on overtime pay. Predictive maintenance drops the need for these pricy emergency call-outs by over 70% since assets are perpetually upheld.
Extended Asset Lifespan
Rather than running assets to failure, predictive maintenance sustains equipment in well-preserved states via prevention-focused upkeep. As machines stay functional for longer lifespans, replacement capital expenditure costs drastically decrease.
Reduced Inventory Levels
With smoother production output, companies don’t have to carry high inventory stockpiles as a buffer against volatility. Holding less excess finished goods liberates tied-up working capital.
Maximized Capacity Usage
If systems frequently shut down for repairs, maximum manufacturing capacity utilization can’t be achieved. Predictive maintenance squeezes out more operational availability to enable full usage of production assets.
Enhanced Safety Assurances
Worn or loose components often precede safety incidents like fires, explosions, toxic leaks, and injuries. Identifying these hazards in advance improves workplace safety through proactive risk reduction. Detailed maintenance records also help organizations meet safety regulations and industry standards.
How to Implement a Predictive Maintenance Program

To successfully launch predictive maintenance, a methodical approach is crucial for smooth implementation and lasting success. Follow this implementation framework:
- Form a Dedicated Team: Establish a designated cross-functional team of reliability specialists, instrumentation experts, data scientists, maintenance technicians, and decision-makers. Lock down stakeholders and budget resources upfront for lasting top-down engagement.
- Audit Critical Assets: Catalog all critical manufacturing assets and evaluate failure points, costs of downtime, repair timelines, and data infrastructure needs. Assess the financial impact of enhancing various systems.
- Deploy Monitoring Sensors: Choose compatible IoT sensors for the assets and operating conditions. Engage technical consultants as needed on specialized instrumentation requirements or data communications. Install sensors on priority machinery first.
- Collect Baseline Data: Accumulate initial performance metrics to derive standard health baselines and acceptable ranges for each monitored parameter. Run assets through diverse production scenarios to log full operational spectra.
- Set Warning Triggers: Program the predictive maintenance software’s diagnostic algorithms to issue warning alerts when metrics edge out of normal thresholds, signaling deterioration. Continuously refine limits to boost detection capabilities over time.
- Respond to Notifications: Require teams to immediately address each notification of impending deviations. Confirm whether signals represent real faults or false alarms. Log findings to keep enhancing analytical accuracy.
- Sustain and Expand: Standardize predictive workflows as integral components of wider maintenance processes. Progressively scale programs by connecting additional sensors and assets once capabilities mature. Consider the use of wearable devices and video analytics. Implement continuous training programs to ensure maintenance teams stay current with evolving technologies and best practices.
- Data Integration and Security: As predictive maintenance systems collect sensitive operational data, ensure robust cybersecurity measures are in place. Implement encryption, access controls, and regular security audits to protect valuable manufacturing intelligence. Consider integrating predictive maintenance data with other business systems, like ERP and quality management, for more comprehensive operational insights.
- Regularly Audit ROI: Track expenses associated with breakdowns, overtime, supplies, and more before and after implementation. Continue quantifying costs avoided through the program to showcase hard dollar savings realized.
Conclusion
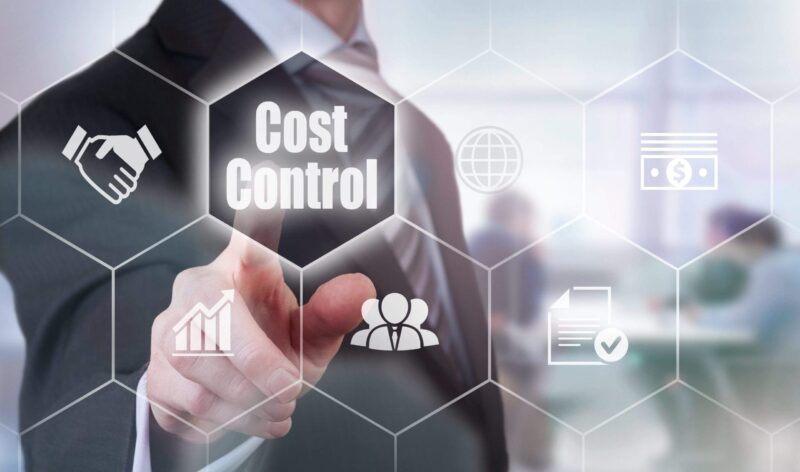
Methodically following these steps for rollout means facilities can establish predictive programs certain to yield formidable expenses reductions through substantial improvements in reliability. The more assets connected and data collected, the greater the cost savings achieved. Implementing a comprehensive predictive maintenance program requires an initial investment and organizational commitment; however, the long-term gains significantly offset the costs. By embracing technology in maintenance, companies can lower operational expenses and gain a competitive edge due to increased efficiency and dependability.